|
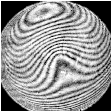
ABERROMETRY
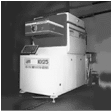
TECHNOLOGICAL
LASERS
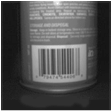
LOGISTICS
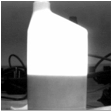
CHEMICAL INDUSTRY
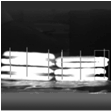
FOOD INDUSTRY
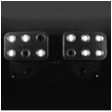
PHARMACOLOGY
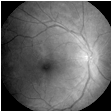
OPHTHALMOLOGY
|
|
|
The
Project is focused on developing and commercializing a novel
smart camera.
The smart camera is a device that combines an image sensor with
an image processing system (including a high-performance DSP)
and an interface for controlling peripherals. Typical fields of
application of smart cameras are optical diagnostics, adaptive
optics, medical equipment, high-precision and high-speed
tracking systems, etc
see «Technical
Specifications»
|
|
|
|
|
The
main objective of this project is manufacturing and
commercializing a novel high-performance smart
camera that
can be used in optical diagnostics, adaptive optics, medical
equipment, high-precision and high-speed tracking systems.
At
present time, conventional image processing systems usually
include analog or digital cameras connected to PCs or industrial
computers by means of special interface boards. Such systems
allow solving a wide range of optical diagnostics and adaptive
optics problems. Examples of such systems are Multispot-250
aberroscope being a part of laser refractive surgery complex Microscan
(PIC, Physics Instrumentation Center RAS), adaptive
multispectral fundus-camera
(ILIT RAS, Institute of Laser and Information Technology RAS),
and many others.
In
adaptive optics systems, systems of laser radiation diagnostics,
optical inspection and medical systems, it is impossible to
achieve ultrahigh performance remaining with the
"PC+camera" platform. A performance of the order of 30
fps can be obtained for sure, but operating frequencies
exceeding 60 Hz cause considerable difficulties. For instance,
when developing an adaptive system with a measurement rate of 77
Hz, the R&D team of Visionica Ltd had to optimize the
software for the specific configuration of a PC and processor.
In other words, such systems are not completely open-ended and
device-independent.
The
accomplished studies resulted in developing unique software that
permits solving a number of actual problems of optical
diagnostics, adaptive optics, and medical diagnostics. We have
designed algorithms of real-time data analysis, which that need
no massive data storage in computer memory. However, it is not
possible to fully utilize the potential of these developments
because of technical limitations introduced by the
"PC+camera" platform. For example, the system has
1,5-2 frame latency caused by buffering that takes place in the
PC and camera interface. This effect reduces the bandwidth of
the adaptive system with a measurement rate of 77 Hz to only
8-10 Hz. Similar problems occur in tracking systems with video
registration, for example, in pupil tracking systems utilized in
ophthalmic and refractive surgery instruments. Such pupil
tracking systems should have a 50-60 Hz bandwidth (200-300 Hz
measurement rate), while the "PC+camera" platform
allows you to get only 10 Hz. As noted above, principal
difficulties occur during the process of data transfer from the
camera to the PC and from the PC memory to the processor. Our
estimations have shown that 70 % of time expenditures of
algorithms used in the above-mentioned problems concern data
transfer between the PC memory and the processor. We should
stress that even the use of the most high-performance computer
platforms doesn't eliminate the problem of latency.
There
are two methods of solving the above problems: the use of
special image-processing DSP-based boards and the development of
smart cameras. In smart cameras, data can directly flow from the
image sensor to the allocated memory of the DSP. Thus, no
buffering delays occur in this case. In our opinion, such a
solution is optimal for constructing high-performance optical
diagnostics and operation systems.
DSPs
with a structure and efficiency adequate to the applications
described above have already entered the market. There are
linear CMOS image sensors with various resolutions and operating
speeds, which are able to cover the whole spread of optical
diagnostics and high-speed tracking problems. The integration of
such a DSP with a CMOS sensor in such a way that to make the
sensor board changeable (in order to vary resolutions and
operating speeds) will provide a universal product that will be
interesting for a wide range of corporate users. |
|
|
|
|
The
smart camera to be created in the framework of the Project will
have the following characteristics:
•
Max. image sensor
resolution:
>1200x1000 pixels
•
Frame
rate: >16
fps
•
Digitization,
at least: 8
bit
•
Processor clock
speed:
500
MHz
•
Processor
width:
64
bits
•
Core
memory:
3 MB
•
Processing
power:
12
GFLOPS
•
Interface
transfer rate to host computer:
> 400
Mb/sec
•
Peripheral
interface:
serial
•
Number of
peripherals:
32
•
Peripherals
interface transfer rate:
> 1
Mb/sec
•
Size:
<60x60x160
mm
•
Weight:
<600 g
•
Power
consumption:
< 12 W
•
Failure time:
> 3000
hours
•
Design: metal case
The software
shall provide:
•
Sensor operation
• Data
transfer from the sensor to the DSP memory
• Data
processing according to uploaded algorithms
• Processed
data transfer to the host computer
• Generation
of operating signals for peripherals
• Transfer
of commands and signals to peripherals
• Diagnostics
and control of operability
According to the above specification, the proposed smart camera
shall provide no less than 200% advantage in efficiency as
compared with the most similar prototype, DVT Legend 554 (DVT
Corporation,
USA).
|
|